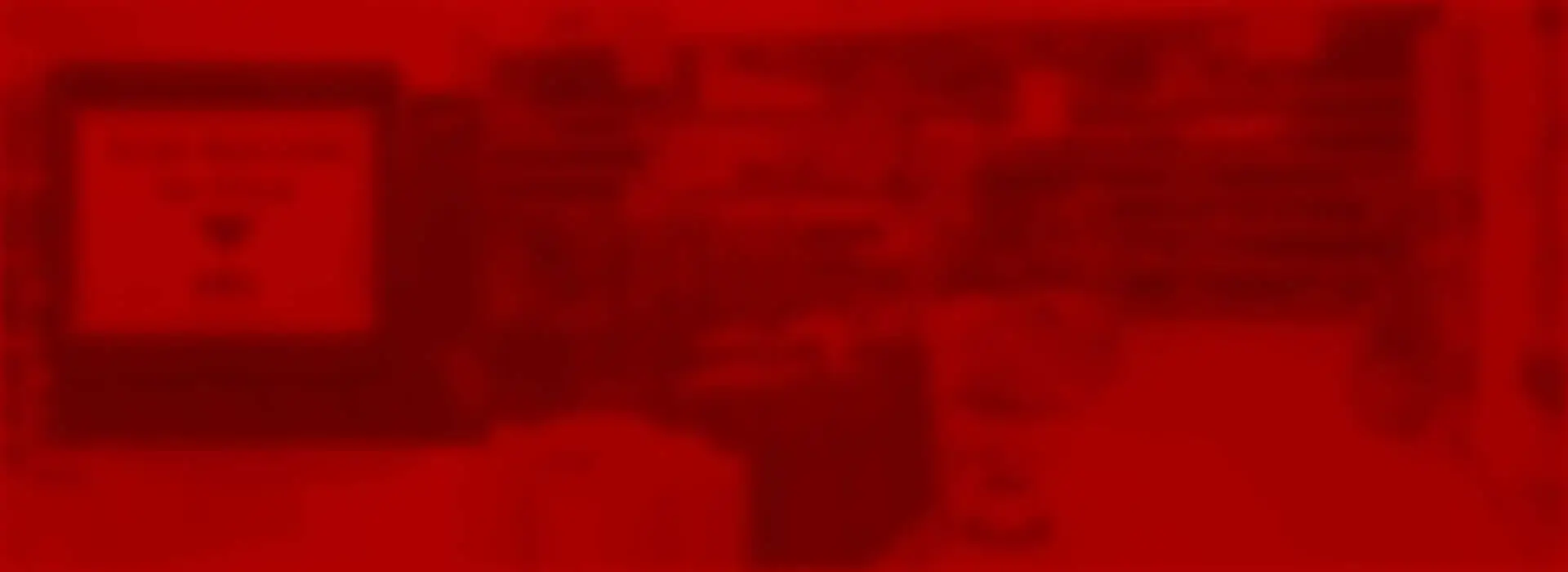
Pick Pack Station
Warehouse Pick and Pack
What is Pick and Pack Fulfillment?
The term “Pick-Pack” can have a broad interpretation when it comes to supply chain applications or activities within the four walls of a warehouse. Some operations refer to it as “pick and pack.” Others “pick, pack, and ship.” Regardless they all simply refer to the process of picking or retrieving the items for an order and then transporting them to an area where they are packaged and prepared for shipping to the customer. The exact way in which this happens depends entirely on the characteristics of the items being picked. Are they cartons that will be picked and then packed onto a pallet? Or are they bags of small parts that will be picked and consolidated into a single box and prepped for shipping? A warehouse scanner is often used to keep track of inventory regardless of the process.
For the purpose of this discussion, we’ll look at an “integrated pick-pack station” that holds all the items that might be included on an order or has a mechanism where the items are delivered to the packing station. The worker is informed on how many of each item goes into a particular order. Those items are picked, scanned with a warehouse barcode scanner and placed into the box. If necessary, packing material is added, the box is sealed and labeled, and then passed on to the shipping department either on an exit conveyor, placed on a cart, or maybe a pallet which will be removed by a forklift.
Pick, Pack, Ship Process Flow
The real work is in making sure the worker knows which items to pick, how many to pick, and then verifying that the item and quantity are correct before going into the box. Paper-based systems are outdated and prone to costly mistakes. Contemporary inventory management systems can generate “pick lists” or “pick tickets” which historically have been printed on paper. But most of these systems can also display the pick lists on a mobile or portable device such as a mobile computer, a forklift terminal/computer, or a stationary kiosk. A scanner can integrate with these systems to update inventory count automatically. The obvious advantage of using an electronic device to access the pick ticket is the elimination of the paper, which serves no purpose after the order is picked. It also eliminates the time lag of getting the information that the order has been picked, into the inventory system. A paper-based system requires some degree of data entry, at some point in the future, to acknowledge order fulfillment.
Improving Picking Accuracy with Real-time Access
When using a computer to access the pick ticket, the worker will not only be instructed what to pick, but they can immediately acknowledge the completion of the pick with a barcode scanner and that information flows in real time. As soon as the order is packed, anyone with access to that information can see it.
Acknowledging the pick may require the worker to press a key on the device or touch a “button” on the screen. Ideally, the pick could be acknowledged with a barcode scanner. This would remove the potential error of pressing the wrong key or touching the wrong button. If the worker was required to scan a barcode on each item, there’s a much better chance that the right quantities of the right items are going into the box. Assuming the order required 3 of one item and 2 of another, if the worker was required to scan 3 barcodes of one item and 2 of the other, right before they went into the box, there is a high probability that the order was picked properly. Furthermore, confirmation of the fulfillment is instantly available. Of course, this type of functionality depends on the capability of the software. But regardless, an electronic means of handling the picking information will always produce better results than a paper-based system.
When using an automated inventory management system, the choice of what device to use at an integrated pick-pack station is very important. Traditionally, integrated pick-pack stations that needed connectivity to an inventory system simply utilized a desktop workstation. But with an integrated Pick-Pack station, space usually comes at a premium. The worker needs space to collect the items ordered and then package them into a box. Often, they even have to assemble the box before packing. The station will also likely include a label printer and a tape gun or tape machine. So again, space can be tight. Even if the computer is tucked under a bench, the monitor must be on the workstation in view of the worker. They will also need somewhere to store a barcode scanner at the workstation. The worker will constantly be picking it up, scanning the items, and putting it down…repeatedly. Monitors, label printers, barcode scanners…they all take up valuable space.
Hands-Free Picking
There is a better solution. The AML Firebird enterprise kiosk is an all-in-one computer with an integrated barcode scanner. Its overall size and weight make it ideal for tabletop mounting with an articulating arm, placing it out of the way of the worker. The 7″ high resolution display offers plenty of viewing area for any pick list, and the integrated downward-facing barcode scanner saves time and worker fatigue. The worker simply presents the item (barcode up) to the Firebird’s barcode scanner before packing the box. The Firebird can be connected to the server over a Wi-Fi network or using a hardwired Ethernet connection. If the Ethernet connection is chosen, the Firebird supports Power-over-Ethernet (PoE) eliminating the need for a power outlet. Powered by Android, the Firebird can run any native Android app (APK) and the browser can connect to any Cloud or On-Premise web-based system. Even legacy apps are accessible using the built-in terminal emulation (TE) client. The Firebird is substantially more robust and durable than a conventional PC workstation, and as a final bonus, it’s Made in America, with U.S. based technical support.
Featured Devices
Firebird
Stationary Computer
Powered by Android®
Integrated 2D Barcode Scanning
7″ Display with Capacitive Touchscreen
Available in portrait or landscape mode
License-free Terminal Emulation
Wi-Fi and BLE 4.2 Smart Ready
Monarch+
Stationary Computer
Powered by Windows®
Integrated 2D Barcode Scanning
10.1″ Display with Capacitive Touchscreen
1.6 GHz Quad Core Processor
Power-over-Ethernet Plus (PoE+)
Optional: Wi-Fi 6 and BLE 5.2 Smart Ready
Questions?
If you have any questions about pricing, requesting demo units or technical specs, submit the form below and our team will be in contact shortly.
About AML
AML was founded in 1983 to respond to a need in the barcode data collection marketplace for high performance, easy-to-use, and cost-effective barcode and data collection products. Our goal is to provide sensible solutions for mission critical activities, to improve efficiency and productivity, and to make barcode data collection applications worry-free.